How Do You Ensure Pressure Vessel Design is Safe and Efficient?
Struggling with reactor safety and performance? You need a vessel that can handle intense conditions without failure, but choosing the right design can be complex and intimidating.
A safe and efficient pressure vessel design starts with selecting the right materials for your specific operating pressure and chemicals. It also involves incorporating critical safety features like relief valves and ensuring a perfect seal to prevent leaks under pressure. These elements are the foundation of reliable performance.
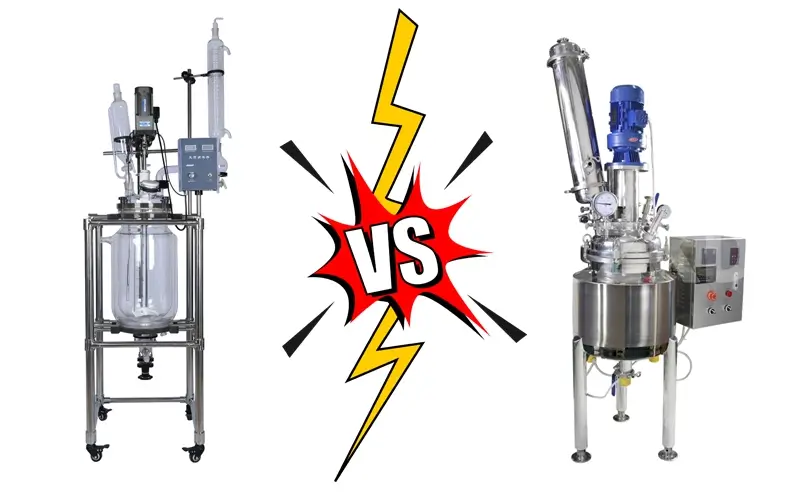
As a manufacturer with over 16 years of experience, I've seen how critical proper reactor design is. It's not just about containing a reaction; it's about controlling it precisely and safely. A well-designed reactor, whether it's glass or steel, is the heart of any successful lab or production process. Getting the design right from the start prevents costly failures and ensures you get consistent, reliable results every time. This is why we focus so much on the details of design for every piece of equipment we build.
What Key Factors Influence Reactor Material Selection?
Choosing between glass and steel feels like a major commitment. You worry that the material you pick might not withstand your chemicals or pressure, leading to costly damage.
Material selection depends on three things: chemical compatibility, operating pressure, and temperature. Borosilicate glass is great for visibility and acid resistance at lower pressures, while stainless steel is essential for high-pressure, high-temperature applications and mechanical strength.
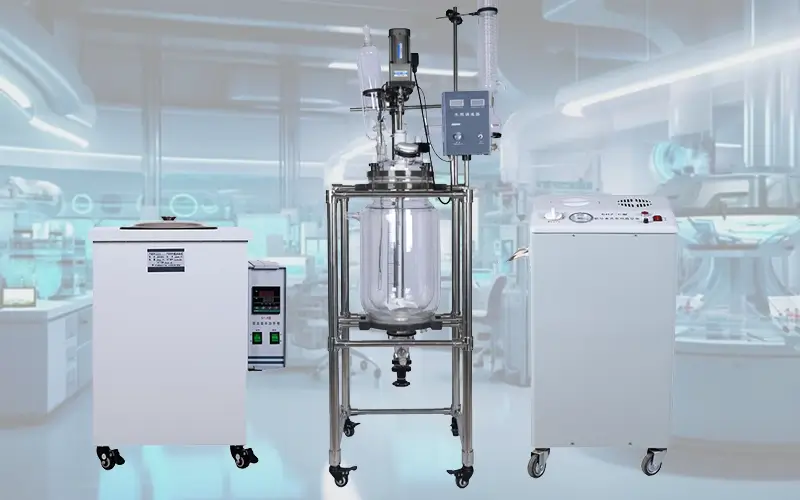
For me, the choice always comes back to the specific job the reactor needs to do. Over the years, I’ve helped thousands of clients navigate this decision. For instance, a university lab doing fundamental research with acids often benefits from a glass reactor. The ability to see the reaction is invaluable for teaching and observation. However, a pilot plant scaling up a high-pressure synthesis process needs the durability and strength of a stainless steel reactor. It's not about one being better than the other; it's about the right tool for the job.
Comparing Glass and Stainless Steel
To make it clearer, let's break down the main differences in a simple way. This can help you see which material fits your needs best.
Feature | Glass Reactor (Borosilicate 3.3) | Stainless Steel Reactor (316L) |
---|---|---|
Pressure Range | Lower pressures (typically up to 45 psig). | High pressures (can exceed 200 bar). |
Temperature Range | Wide, but sensitive to rapid changes (thermal shock). | Excellent for very high and very low temperatures. |
Chemical Resistance | Excellent against most acids and chemicals. | Good, but can be susceptible to corrosion from certain strong acids. |
Visibility | Fully transparent, allowing for visual monitoring. | Opaque, requires instruments to monitor the reaction. |
Durability | Prone to mechanical damage if not handled with care. | Very strong and resistant to physical impact. |
How Does Sealing Affect Pressure Reactor Safety?
An improper seal can be disastrous. You might worry about leaks of hazardous materials, loss of pressure, or even catastrophic failure, making every operation a high-risk gamble.
A perfect seal is critical for safety because it prevents leaks of toxic or flammable substances and maintains the required pressure for the reaction. Gaskets, flanges, and proper bolt tightening work together to create a secure barrier, ensuring both operational stability and personnel safety.
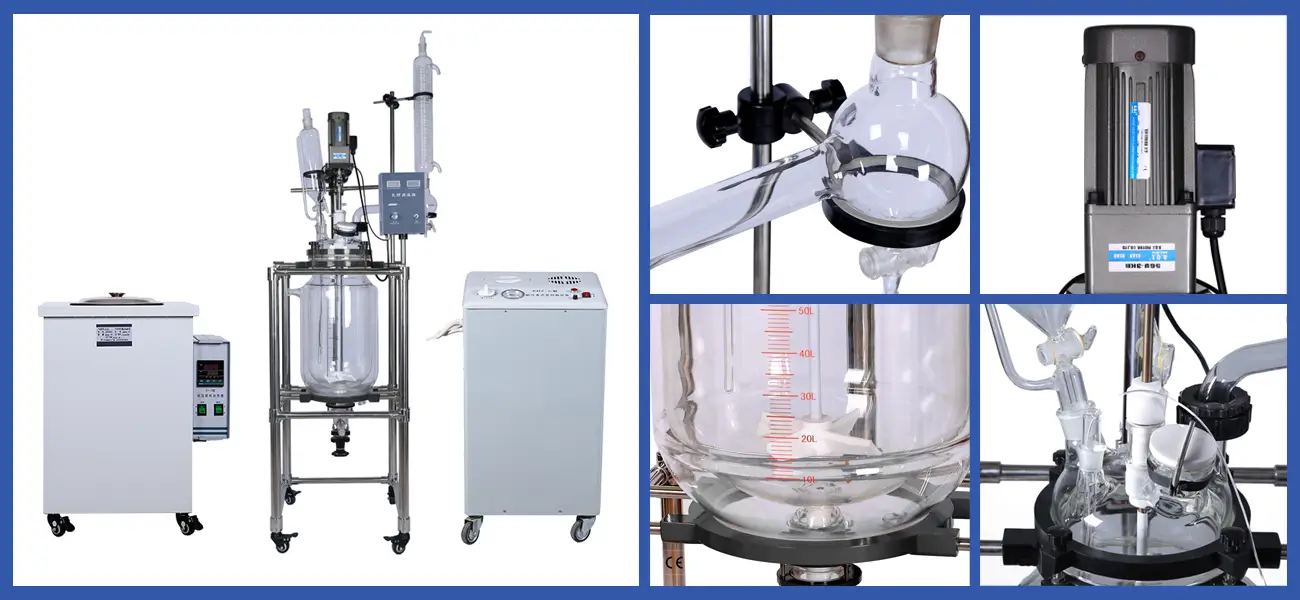
I remember a client who was struggling with inconsistent results. After talking with them, we suspected a sealing issue. Even a small, slow leak can throw off a pressure-sensitive reaction. The problem is that the seal isn't just one part; it's a complete system. You have the flange surfaces, the gasket material, and the force from the bolts all working together. If one part is wrong—like an incompatible gasket material or uneven bolt pressure—the whole system fails. That’s why we machine our flange surfaces to be perfectly flat and provide detailed instructions on tightening sequences. It’s a small detail that makes a huge difference in safety and reliability. A reliable seal is the first line of defense in any high pressure reactor.
Components of an Effective Seal
To really understand it, think of these three parts:
Flanges: These are the rims that connect parts of the reactor. Their surfaces must be perfectly flat and clean to ensure a good seal.
Gaskets: This is the material that sits between the flanges. It compresses to fill any tiny imperfections and creates the actual barrier. The material (like PTFE) must be compatible with your chemicals and temperature.
Bolts/Clamps: These provide the force needed to compress the gasket and hold the flanges together. The force must be applied evenly to prevent leaks.
What Safety Features are Absolutely Essential?
Running a pressurized reaction without the right safety features is nerve-wracking. You are constantly concerned about what could go wrong, from over-pressurization to a runaway reaction.
Essential safety features include a pressure relief valve to automatically release excess pressure and a rupture disk as a backup failure point. Real-time pressure and temperature monitoring with alarms and an emergency shutdown system are also critical for preventing accidents.

Safety is not something you can add on later; it has to be built into the design from the very beginning. From our experience, the most important features are the ones that work automatically, without needing someone to react in time. The pressure relief valve is a perfect example. It's a simple mechanical device that is set to a specific pressure. If the reactor exceeds that pressure, the valve opens and vents the excess. The rupture disk is even simpler—it's a thin metal disk designed to burst at a set pressure, providing a final, guaranteed release path. We insist on including these on every pressure system we build. It provides peace of mind and ensures that even in a worst-case scenario, the vessel itself will not fail catastrophically.
Key Safety Mechanisms Explained
Here’s a quick look at the main safety systems and what they do:
Pressure Relief Valve: Your first line of defense. It automatically opens when pressure gets too high and closes when it returns to a safe level.
Rupture Disk: A one-time-use backup. If the relief valve fails, this disk will burst to prevent an explosion.
Pressure Gauge: A simple visual indicator of the internal pressure, allowing for constant monitoring.
Temperature Controller: Works with a heating/cooling jacket to keep the reaction at the set temperature, preventing dangerous temperature spikes.
Conclusion
In summary, safe pressure vessel design combines the right material choice, a perfect seal, and essential safety features. This ensures your reactions are efficient, reliable, and secure.